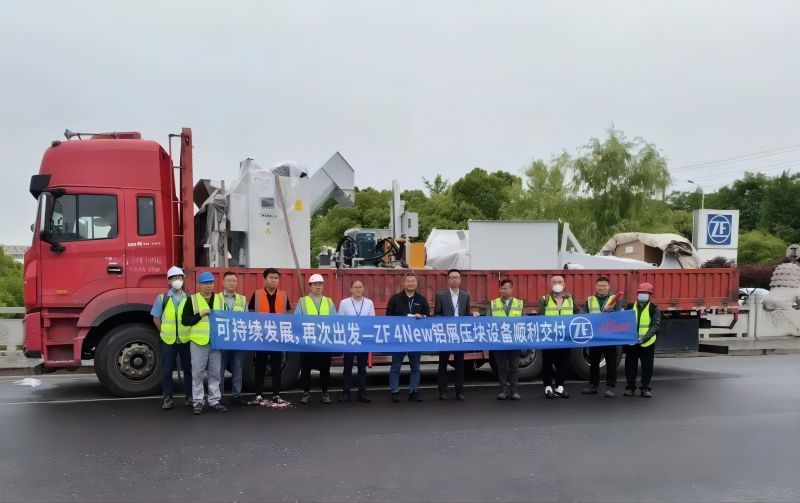
Project Background
ZF Zhangjiagang Factory is a key regulatory unit for soil pollution and a key environmental risk control unit. Every year, the aluminum scraps produced by the aluminum pliers and main cylinder machining in Zhangjiagang factory contain a large amount of cutting fluid, with an annual output of about 400 tons of waste liquid, accounting for 34.5% of the hazardous waste in the entire park, and the waste liquid accounts for 36.6%. A large amount of waste liquid cannot be effectively disposed of and utilized, which not only leads to resource waste, but also may cause serious environmental pollution incidents during the waste transfer process. To this end, the company's management team focused on sustainable development and proposed emission reduction targets for corporate environmental responsibility, and immediately launched the aluminum scrap crushing waste liquid recycling project.
On May 24, 2023, the customized 4New aluminum chip aluminum briquetting and cutting fluid filtration and reuse equipment for ZF Zhangjiagang factory was officially delivered. This is another major measure aimed at environmental protection, regeneration, environmental protection, and sustainable development, following the solar photovoltaic project and vacuum distillation sewage treatment project, to assist ZF Group's "next generation travel" sustainable development strategy
System advantages
01
The volume of slag and debris is reduced by 90%, and the liquid content in the blocks is less than 4%, greatly reducing the efficiency of on-site stacking and storage, and improving the on-site environment
02
This section mainly analyzes the subjective and objective conditions, favorable and unfavorable conditions, as well as the working environment and foundation of the work.
03
The ME department uses the idle machine tool cutting fluid filtration and reuse equipment after technological transformation to connect the aluminum chip pressing machine to filter and reuse the cutting fluid after aluminum chip pressing, with a purification and reuse rate greater than 90%
Outlook for Achievements
With the smooth delivery of the equipment and subsequent installation and debugging, it is expected to be officially put into use in June. The cutting fluid after pressing is filtered and reused through the waste liquid filtration system, and 90% is reused in the production line, greatly reducing the risk of soil environmental pollution and the overall cost of using metal processing fluid.
Post time: Jun-06-2023